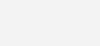
Nov 24 2023
/
Lean Manufacturing Principles for Efficient Industrial Production
Lean Manufacturing has emerged as a pivotal strategy in the realm of industrial production, revolutionizing how companies approach efficiency and productivity. Originating from Japan, this methodology has gained global prominence for its ability to streamline processes, minimize waste, and enhance overall operational excellence.
In industrial production, efficiency is the key to staying competitive. Lean Manufacturing stands as a beacon, guiding companies toward optimal performance and resource utilization. Let’s delve into the world of Lean principles and how they contribute to efficient industrial production.
Origins of Lean Manufacturing
Historical Background
The roots of Lean Manufacturing trace back to post-World War II Japan. Scarce resources prompted innovative thinking, leading to the development of principles that would later become the foundation of Lean.
Key Contributors to Lean Principles
Visionaries like Taiichi Ohno and Shigeo Shingo played instrumental roles in formulating and refining Lean Manufacturing concepts. Their insights continue to shape the manufacturing landscape today.
Core Principles of Lean Manufacturing
1. Just-in-Time (JIT) Production
Lean emphasizes JIT, ensuring that components are produced or delivered precisely when needed. This minimizes inventory costs and reduces the risk of overproduction.
2. Continuous Improvement (Kaizen)
Kaizen, meaning continuous improvement, is at the heart of Lean. Companies embracing Kaizen foster a culture of ongoing refinement, propelling them toward excellence.
3. Respect for People
Lean Manufacturing places a high value on human capital. Creating a work environment that respects and empowers employees is crucial for sustained success.
4. Value Stream Mapping
Understanding the entire production process is vital. Value Stream Mapping helps identify and eliminate inefficiencies in the workflow, optimizing the value delivered to the customer.
5. Pull System
A Pull System ensures that production is demand-driven, preventing overproduction and reducing excess inventory.
6. Kanban System
Kanban, a visual management system, enhances communication and efficiency by signaling when to produce or replenish materials.
Implementation of Lean Manufacturing
Introducing Lean principles into an organization is a strategic process that requires careful planning and execution. Here are the key steps to successfully implement Lean principles:
1. Leadership Alignment and Commitment
Before embarking on a Lean journey, ensure that top-level leadership is not only aware of Lean principles but fully committed to their implementation. Leaders set the tone for the entire organization, and their commitment is crucial for overcoming resistance to change. Hold discussions, workshops, or training sessions to align leadership with the philosophy and benefits of Lean Manufacturing.
2. Employee Training and Involvement
The success of Lean principles relies heavily on the active involvement of employees at all levels. Provide comprehensive training sessions to familiarize staff with Lean concepts, tools, and methodologies. Encourage a culture of continuous improvement by fostering an environment where employees feel empowered to identify and address inefficiencies in their daily work. This involvement ensures a smoother transition and a higher likelihood of sustained Lean practices.
3. Identify and Map Value Streams
Understanding the value streams within your organization is fundamental to Lean Manufacturing. Conduct a thorough analysis of your current processes to identify value-adding activities and eliminate non-value-adding ones. Value Stream Mapping (VSM) is a powerful tool for visualizing the entire production process, helping you identify areas of waste, redundancy, and inefficiency. This mapping sets the foundation for targeted improvements and optimization.
4. Implement Pilot Projects
Rather than attempting a full-scale Lean transformation immediately, consider implementing pilot projects in specific areas of your organization. These pilot projects serve as practical testing grounds for Lean principles, allowing you to assess their effectiveness in a controlled environment. Measure key performance indicators (KPIs) and gather feedback from employees involved in these projects. This incremental approach allows for adjustments based on real-world results before scaling Lean practices throughout the organization.
5. Establish Continuous Improvement Mechanisms
Continuous improvement is at the core of Lean Manufacturing. Once Lean principles are introduced, establish mechanisms for ongoing evaluation and enhancement. Regularly review performance metrics, gather feedback from employees, and conduct periodic assessments of Lean practices. Encourage a culture where everyone, from the shop floor to the boardroom, is engaged in identifying opportunities for improvement. This iterative approach ensures that Lean principles become ingrained in the organizational culture, leading to sustained efficiency gains.
Benefits of Lean Manufacturing
From increased efficiency to cost savings, organizations implementing Lean principles experience a wide range of benefits. Let’s delve into the specific advantages of Lean Manufacturing in the context of industrial production:
Enhanced Operational Efficiency
At the core of Lean Manufacturing is the pursuit of efficiency. By eliminating wasteful processes, reducing unnecessary steps, and optimizing workflows, industrial production becomes more streamlined. This heightened efficiency enables organizations to produce more output with the same or fewer resources, ultimately maximizing operational capabilities.
Reduction in Waste
Lean principles actively target various forms of waste, including overproduction, excess inventory, defects, and unnecessary motion. By identifying and eliminating these sources of waste, industrial production becomes more resource-efficient. This reduction in waste not only contributes to cost savings but aligns with sustainable practices, reducing the environmental impact of manufacturing processes.
Improved Product Quality
Efficiency gains in Lean Manufacturing often result in improved product quality. By identifying and addressing the root causes of defects, organizations can enhance the overall quality of their manufactured goods. Consistently producing high-quality products not only satisfies customer expectations but also reduces the need for rework and warranty claims.
Cost Savings
Lean Manufacturing leads to cost savings through various avenues. Reduced inventory carrying costs, lower operational expenses, and minimized defects contribute to overall cost efficiency. These cost savings enhance the financial stability of organizations engaged in industrial production.
Shorter Lead Times
The just-in-time (JIT) production approach in Lean Manufacturing minimizes the time between production and delivery. This not only reduces the need for large inventories but also shortens lead times. For industrial production, shorter lead times mean greater agility in responding to market demands, reducing the risk of overproduction and optimizing resource utilization.
Conclusion
In conclusion, Lean Manufacturing offers a transformative approach to industrial production, emphasizing efficiency, waste reduction, and continuous improvement. Embracing Lean principles positions companies for long-term success in an ever-evolving market.