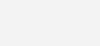
Jul 01 2025
/
Three production bottlenecks ERP helps you eliminate
Running a factory smoothly matters more than ever. When your production stalls or slows down, costs rise, and customers get frustrated. That’s why fixing bottlenecks is crucial for staying competitive. Production hiccups can waste time, money, and trust. Luckily, Enterprise Resource Planning (ERP) systems can help you spot and fix these issues fast. Recent data shows companies earn up to 25% more efficiency when they use ERP to streamline manufacturing. Let’s explore how ERP can unlock better manufacturing flow by eliminating the top three bottlenecks.
Understanding Production Bottlenecks in Manufacturing
What Are Production Bottlenecks?
Think of a production line like a pipe. If one spot slows down, everything behind it backs up. That slow point is a bottleneck. In manufacturing, bottlenecks are stages or machines that limit overall output. They stop your factory from producing at full speed. When a machine breaks, or workers are idle, production shrinks.
Common Causes of Bottlenecks
- Outdated machinery or technology: Old machines break often and run slow.
- Inefficient inventory management: Not enough raw materials cause delays; too much stock ties up cash.
- Poor scheduling and resource allocation: Overlapping tasks or missing deadlines create idle time.
- Supply chain variability: Raw materials arriving late or in bad quality slows everything down.
Impact of Bottlenecks on Business Performance
Bottlenecks lead to longer lead times and missed delivery dates. This results in unhappy customers and lost sales. Operational costs go up because resources are wasted. Overall, business suffers when production doesn’t run smoothly.
How ERP Systems Identify and Address Production Bottlenecks
Real-Time Data Visibility and Monitoring
ERP software provides instant updates on machines, orders, and inventory. You see what’s happening now, not weeks ago. For example, SAP ERP offers dashboards showing live production stats. This helps managers act fast before small issues become big problems.
Advanced Planning and Scheduling Capabilities
Modern ERP systems help plan the best use of machines and staff. They can shift schedules as needed with just a click. If a machine breaks, the system suggests alternate plans. Predictive analytics forecast potential slowdown points. These tools make your production more agile.
Integrated Inventory and Supply Chain Management
ERP connects your supply chain directly to production. You always know the right amount of raw materials to keep in stock. This prevents shortages or excess storage. Timely procurement ensures your workflow stays steady.
Top Three Production Bottlenecks ERP Helps You Eliminate
1. Equipment Downtime and Maintenance Delays
Causes and consequences
Unexpected breakdowns disrupt the flow. When a machine goes down without warning, production stops. Delivery schedules get thrown off, and costs skyrocket due to urgent repairs.
How ERP solutions help
ERP integrates with the Internet of Things (IoT) sensors. These sensors monitor equipment health constantly. When they detect trouble, ERP sends alerts. Predictive maintenance schedules replace guesswork, keeping your machines running.
Actionable Tips
- Use ERP to plan regular maintenance during slow periods.
- Train staff to monitor equipment data via ERP dashboards.
- Keep spare parts ready based on predictive insights.
2. Inefficient Production Scheduling
Causes and consequences
Poor scheduling happens when tasks overlap or rely on unrealistic timelines. You get workers waiting idle or miss delivery deadlines. This wastes time and money.
How ERP solutions help
ERP offers dynamic scheduling tools that adapt instantaneously. If a task finishes early, the system shifts the next step forward. Simulation features help plan the smartest sequence in advance. Better schedules mean less downtime and faster delivery.
Actionable Tips
- Regularly review schedules with ERP reports.
- Use analytics to identify recurrent delays.
- Adjust plans based on real-time data for more accuracy.
3. Material Shortages and Inventory Overstock
Causes and consequences
Demand forecasts can be off, causing too little or too much stock. Stockouts halt production; overstock ties up cash and space.
How ERP solutions help
ERP’s demand forecasting uses past data to predict needs accurately. Just-in-time inventory management keeps materials coming as needed. This reduces waste and prevents delays.
Actionable Tips
- Set automatic reorder points in your ERP system.
- Audit safety stock levels regularly.
- Align procurement with actual production needs through ERP data.
Additional Benefits of ERP in Manufacturing Optimisation
ERP isn’t just about fixing bottlenecks. It also boosts product quality, improves teamwork across departments, and helps make smarter choices. With detailed traceability, you can quickly pinpoint the roots of quality issues. Collaboration tools break down silos, so everyone works together. Data-driven decisions lead to continuous improvement.
Conclusion
Identifying and fixing production bottlenecks can seriously boost your factory’s performance. ERP systems offer powerful tools for continuous monitoring, smart scheduling, and inventory management. They turn production from a guessing game into a well-oiled process. Keep an eye on equipment health, plan schedules wisely, and control your supply chain tightly. These steps help you eliminate delays and grow your business. Now is the time to evaluate your current processes. Consider implementing an ERP to unlock maximum efficiency and stay ahead in manufacturing.