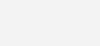
Jul 23 2024
/
Staying Ahead in Smart Manufacturing: Latest Trends and Innovations
Smart manufacturing is rapidly transforming the landscape of industrial production, integrating advanced technologies to create highly efficient, flexible, and sustainable manufacturing processes. As industries strive to stay competitive in a dynamic market, embracing the latest trends and innovations in smart manufacturing is essential. This article delves into the key trends and innovations driving the future of manufacturing.
1. Industrial Internet of Things (IIoT)
The Industrial Internet of Things (IIoT) continues to be a cornerstone of smart manufacturing. IIoT connects machines, devices, and systems, enabling seamless communication and data exchange across the production floor. This connectivity facilitates real-time monitoring, predictive maintenance, and optimized asset utilization.
Key Benefits:
Improved Efficiency: IIoT allows for real-time tracking of production metrics, helping identify bottlenecks and streamline operations.
Predictive Maintenance: By analyzing data from sensors, manufacturers can predict equipment failures and schedule maintenance proactively, reducing downtime.
Enhanced Quality Control: IIoT enables continuous monitoring of product quality, ensuring defects are detected early in the production process.
2. Artificial Intelligence and Machine Learning
Artificial Intelligence (AI) and Machine Learning (ML) are revolutionizing manufacturing by providing insights that drive smarter decision-making. AI algorithms analyze vast amounts of data to identify patterns, optimize processes, and improve overall efficiency.
Key Applications:
Predictive Analytics: AI and ML can forecast demand, optimize inventory levels, and reduce wastage.
Quality Assurance: Machine learning models can detect anomalies in real-time, ensuring high-quality production.
Robotic Process Automation (RPA): AI-driven robots can handle repetitive tasks, increasing productivity and reducing human error.
3. Additive Manufacturing (3D Printing)
Additive manufacturing, commonly known as 3D printing, is transforming traditional manufacturing processes. It allows for the creation of complex, customized parts with minimal material waste.
Advantages:
Design Flexibility: 3D printing enables the production of intricate designs that would be impossible with conventional methods.
Cost Efficiency: Reducing the need for molds and tooling lowers production costs.
Sustainability: Additive manufacturing uses only the necessary amount of material, minimizing waste.
4. Digital Twin Technology
Digital twin technology creates a virtual replica of a physical asset or process, allowing manufacturers to simulate and optimize operations before implementing them in the real world. This technology enhances decision-making and reduces the risk of costly errors.
Key Benefits:
Simulation and Testing: Digital twins enable manufacturers to test various scenarios and optimize processes without disrupting actual production.
Predictive Maintenance: By monitoring the digital twin, manufacturers can predict and address issues before they affect the physical asset.
Enhanced Collaboration: Digital twins facilitate collaboration among different teams by providing a shared, real-time view of the production process.
5. Advanced Robotics and Automation
The integration of advanced robotics and automation is a hallmark of smart manufacturing. Robots are becoming more intelligent, collaborative, and capable of performing complex tasks with precision.
Innovations:
Collaborative Robots (Cobots): Cobots work alongside human workers, enhancing productivity and safety.
Autonomous Mobile Robots (AMRs): AMRs can navigate and transport materials within the production facility autonomously.
Flexible Automation: Advanced robotics systems can adapt to different tasks, increasing the flexibility of manufacturing processes.
6. Edge Computing
Edge computing involves processing data closer to the source of data generation, reducing latency and bandwidth usage. In manufacturing, edge computing enables real-time analytics and decision-making at the production floor level.
Key Advantages:
Reduced Latency: By processing data locally, edge computing minimizes delays, crucial for time-sensitive applications.
Enhanced Security: Keeping data at the edge reduces the risk of data breaches during transmission.
Scalability: Edge computing supports scalable and distributed manufacturing operations.
7. Cybersecurity
As manufacturing becomes increasingly connected, the need for robust cybersecurity measures is paramount. Protecting sensitive data and ensuring the integrity of production systems is critical to maintaining operational continuity.
Best Practices
Regular Security Audits: Conducting frequent security assessments helps identify and address vulnerabilities.
Employee Training: Educating employees on cybersecurity best practices reduces the risk of human error.
Advanced Security Solutions: Implementing multi-layered security measures, such as encryption and intrusion detection systems, enhances protection.
Conclusion
Staying ahead in smart manufacturing requires continuous innovation and adaptation to emerging trends. By leveraging IIoT, AI, additive manufacturing, digital twins, advanced robotics, edge computing, and robust cybersecurity, manufacturers can achieve unprecedented levels of efficiency, flexibility, and sustainability. Embracing these technologies not only enhances competitiveness but also paves the way for a smarter, more resilient manufacturing future.
If you have any questions or would like to learn more about how to stay ahead in smart manufacturing with the latest trends and innovations, contact us today! Our experts are ready to help you transform your manufacturing processes and achieve new levels of efficiency and success.
Contact us at enquiry@phitomas.com