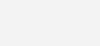
Jul 02 2025
/
Shop Floor to Top Floor Data Connectivity: Why It Matters for Modern Manufacturing
Connectivity in manufacturing has become the backbone of success today. Companies that link shop floor data with top floor decisions can cut costs, improve quality, and stay ahead of competitors. This flow of real-time data allows factories to be smarter, faster, and more flexible. As industries shift towards digital, understanding why data connectivity matters is more important than ever. It’s not just about collecting data — it’s about turning that data into real action.
The Evolution of Manufacturing Data Connectivity
From Isolated Machines to Integrated Systems
In the past, factories operated with standalone machines. Each unit worked its own way, with limited information sharing. This created lots of silos, making it hard to see the full picture. Data was trapped inside machines and rarely used to improve processes. As a result, inefficiency and errors ran high, costing millions over time.
The Rise of Industrial IoT and Smart Factories
Now, devices connect through the Internet of Things (IoT). Smart sensors gather real-time data and send it to central systems. Factories with Industry 4.0 setups can monitor everything from machine wear to energy use. Think of it like giving your factory a nervous system, able to detect issues early and adjust on the fly.
Key Statistics on Digital Transformation Adoption
According to recent surveys, over 70% of manufacturers are adopting connected technology in some form. Companies with better data flow see productivity improvements of up to 30%. It’s clear: connected factories are more competitive, leading to faster production and happier customers.
Benefits of Connecting Shop Floor Data to Top Floor
1. Enhanced Decision-Making and Business Agility
Having all data at your fingertips means quick, informed decisions. If a machine starts showing signs of failure, maintenance can be scheduled before a breakdown occurs. This ability to act instantly boosts overall agility. For example, some plants have reduced downtime by 20% after connecting their data systems.
2. Operational Efficiency and Cost Reduction
Data helps reveal bottlenecks and waste in processes. When factories analyse real-time data, they optimise energy use, reduce downtime, and cut maintenance costs. Imagine saving thousands by fixing small issues before they turn big. These gains add up, saving money and time.
3. Improved Quality Control and Compliance
Traceability is a huge plus. When data is recorded at every step, quality issues become easier to spot and fix early. This also makes regulatory reporting straightforward. Some manufacturers have doubled their quality compliance scores by using integrated data systems to track products from start to finish.
4. Innovation and New Business Models
Access to data opens doors for new ways to grow. Customisation, for example, becomes easier when factories collect customer data and feedback. They can quickly develop products tailored to user needs. Some firms have created entirely new revenue streams by selling insights derived from their manufacturing data.
Critical Components of an Effective Data Connectivity Infrastructure
Network Architecture and Data Integration Platforms
To connect old and new systems, strong networks are essential. Industrial Ethernet, 5G networks, and edge computing help transfer data quickly and reliably. Good integration platforms ensure legacy machines speak the same language as modern IoT devices
Data Management and Analytics Tools
Collected data needs to be stored, cleaned, and analysed. Advanced tools use artificial intelligence to spot patterns. These insights predict when a machine might fail or suggest process improvements. This turns raw numbers into useful knowledge.
Cybersecurity and Data Privacy
Securing data prevents cyber attacks and protects sensitive information. Strong firewalls, encryption, and access controls are vital. Factories must follow data standards too, avoiding penalties or legal issues linked to breaches.
Challenges and Solutions in Implementing Shop Floor to Top Floor Connectivity
Technical Challenges
Many factories face hurdles with old equipment that won’t connect easily. Handling large data streams in real time can also be tough without proper systems. Upgrading or adding new hardware often requires significant investment.
Organisational and Cultural Barriers
Sometimes staff resist new technology. Change can be seen as a threat, not an opportunity. To succeed, companies need to train workers and promote a culture that embraces innovation. Clear communication helps teams see the benefits.
Best Practices for Successful Implementation
Start small with pilot projects. This reduces risk and shows value early. Partnering with technology experts or vendors can smooth the rollout. Regular reviews and updates keep the system working well and adapting to new needs.
Future Trends and Innovations in Manufacturing Data Connectivity
Increased Use of 5G and Edge Computing
Faster data transfer makes factories more responsive. 5G can connect multiple devices simultaneously, while edge computing processes data right where it’s collected. This reduces delays and improves decision speed.
Advanced Analytics and AI Integration
Future factories will be even smarter. AI algorithms will automatically optimise processes, predict equipment failures, and improve product quality. This kind of self-adjusting system cuts waste and boosts output.
Blockchain and Secure Data Sharing
Blockchain helps make supply chains more transparent. It creates a secure, trusted record of movements, quality, and ownership. This can reduce fraud, strengthen trust, and simplify complex logistics.
Sustainability and Data-Driven Environmental Initiatives
Factories will use data to monitor energy, emissions, and waste. Real-time insights allow quicker action to reduce environmental impact. This supports companies’ sustainability goals and can even lower operational costs.
Conclusion
Connecting shop floor data to top floor decisions is no longer optional — it’s essential. It leads to improved efficiency, better quality, and new opportunities for growth. As technology evolves, factories must invest wisely in digital infrastructure. Embracing these changes is the key to staying competitive in today’s fast-changing manufacturing world. The future of manufacturing depends on how well we connect, analyse, and act on data. Now’s the time to make that leap.