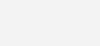
Jul 21 2025
/
Is Your Data Collection Driving ROI?
In today’s manufacturing world, data isn’t just an add-on — it’s the lifeblood of efficiency and growth. More factories are now turning to connected sensors, robots, and systems that gather information around the clock. Industry 4.0 has accelerated this shift, making data collection more vital than ever. Companies that harness this data can cut costs, speed up production, and stand taller against competitors. But the real question is: Are manufacturers truly using their data to boost return on investment (ROI)? Without a clear, strategic plan, data can turn into just background noise. The key lies in collecting the right data and making smart decisions based on it.
The Role of Data Collection in Modern Manufacturing
Understanding the Shift Towards Data-Driven Manufacturing
Manufacturing has gone through a big change. It used to be about machines and manual checks. Now, it’s about smart factories that use digital tools to improve everything. This shift brings a flood of data from sensors, robots, and systems that monitor operations 24/7. Imagine a factory where machines tell you when they need fixing just before breaking down—that’s the power of real-time data. Companies embracing this change see huge improvements in productivity and cost savings.
Types of Data Collectible in Manufacturing Environments
Manufacturers gather many types of data, each offering different insights:
- Operational data: How well machines perform and what they produce daily.
- Quality data: Defect rates, inspection results, and product accuracy.
- Supply chain data: Inventory levels, shipment schedules, and logistics.
- Employee data: Workforce productivity and safety records.
Each set of data plays a role. When combined, they paint a full picture of how a factory runs.
Benefits of Effective Data Collection
Collecting data correctly delivers powerful results:
- Downtime drops through predictive maintenance, fixing issues before they cause delays.
- Quality improves when problems are spotted early.
- Supply chains become more responsive, adapting quickly to changes.
- Real-time info helps measure ROI fast, showing what works and what doesn’t.
With good data, manufacturing becomes smarter and more competitive.
Evaluating Your Manufacturing Data Collection Strategy
Key Components of an Effective Data Strategy
To get the most from data, a plan must be clear. It should include:
- Clear goals that match business ambitions.
- Comprehensive data gathered across all processes.
- Combined data from different sources for a full view.
- Focus on data accuracy and quality to trust the insights.
Without these pieces, data can lead to confusion rather than clarity.
Common Gaps in Manufacturing Data Collection
Many companies face pitfalls in their data efforts:
- Data may be incomplete due to separate, siloed systems.
- Older or faulty inputs lead to wrong conclusions.
- Lacking real-time monitoring means missed opportunities.
- Often, collected data isn’t fully used for decisions.
Identifying these gaps is the first step to fixing them.
Actionable Tips to Optimise Data Collection
To improve, consider:
- Conduct a thorough data audit to find missing or faulty information.
- Invest in integrated IoT platforms that connect all systems smoothly.
- Train staff to handle data entry and interpretation properly.
- Set KPIs that measure data quality and impact on performance.
Continuously refining your data process enables smarter actions and better results.
Analyzing Data to Maximise ROI
Turning Data into Actionable Insights
Once data is collected, the goal is clarity. Use analytics tools, dashboards, and reports to spot bottlenecks and inefficiencies. For example, a manufacturer might see that a machine’s downtime causes lost production and fix it proactively. One factory increased ROI by adopting predictive analytics, reducing outages significantly. Clear insights lead directly to smarter decisions that improve overall profit.
Leveraging Advanced Technologies
Next-level tech such as machine learning or AI can identify patterns humans might miss. Real-time dashboards reveal issues immediately, allowing quick fixes. For example, AI-driven systems now inspect quality more accurately than human eyes, catching defects early and reducing waste. The more you use these tools, the more your ROI can grow.
Measuring ROI from Data Initiatives
It’s not enough to collect and analyse data—measurement matters. Key metrics include:
- Less machine downtime
- Fewer product defects
- Increased output or throughput
Doing a cost-benefit analysis of your data tools shows if your investment pays off. Keep track of these KPIs regularly and adjust strategies for ongoing improvement.
Challenges and Risks in Manufacturing Data Collection
Data Privacy and Security Concerns
With data growing every day, security matters. Sensitive information like proprietary processes or safety data must be protected. Falling short risks breaches or compliance issues.
Managing Data Complexity
As data volume grows, so does complexity. Handling different formats, sources, and large data sets can be overwhelming. Ensuring data is consistent and reliable requires effort and good systems.
Overcoming Resistance to Change
Not everyone is eager to adopt new tech. Staff may resist due to fear or unfamiliarity. Clear communication, training, and showing how data helps make jobs easier can turn resistance into support.
Future Trends in Manufacturing Data and ROI
The future promises faster data processing with 5G and edge computing. Digital twins — virtual models of real factories — will help simulate improvements. Autonomous systems will make decisions without human input, trimming waste even more. With each step, the potential ROI boosts grow. Staying ahead means embracing these trends early.
Conclusion
Using data effectively isn’t an option — it’s a necessity for manufacturing growth. Align your strategy with your business goals, invest in the right technology, and keep refining your approach. Regularly review your data practices to stay competitive and maximise ROI. The smarter your data collection, the more your factory can grow, adapt, and succeed in a changing world. Take control of your data today and unlock the full potential behind every decision.tion? Start by assessing your current systems and identifying the integration opportunities that will deliver the highest impact for your business growth objectives.