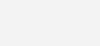
Mar 14 2025
/
Hidden Costs in Semiconductor Manufacturing & How to Optimize Them
Semiconductor manufacturing is a high-stakes industry where even minor inefficiencies can lead to significant financial losses. From supply chain disruptions and rising material costs to production bottlenecks and compliance challenges, these hidden expenses can quietly erode profitability. Identifying and addressing these challenges is critical for manufacturers aiming to stay competitive in an increasingly complex global market.
Key Hidden Costs in Semiconductor Manufacturing and How to Address Them
1. Supply Chain Bottlenecks and Logistical Delays
The semiconductor supply chain is highly interconnected, relying on a complex web of suppliers, raw materials, and global trade routes. Any disruption can result in:
- Extended lead times causing production slowdowns
- Costly expedited shipping to meet urgent demands
- Revenue losses from stock shortages and delayed product launches
Optimization Strategy: To mitigate these risks, implement AI-powered supply chain management for real-time visibility and proactive risk mitigation. Additionally, predictive analytics helps forecast disruptions, while diversifying supplier networks further reduces dependency on single-source suppliers.
2. Rising Material and Energy Costs
Semiconductor production depends on rare and expensive materials, such as silicon wafers and gallium arsenide. Moreover, energy-intensive fabrication processes significantly drive up operational expenses.
Optimization Strategy: Reducing costs requires adopting energy-efficient manufacturing and leveraging AI-driven material procurement optimization. Furthermore, exploring alternative materials and sustainable sourcing can help stabilize costs in volatile markets.
3. Unplanned Downtime and Production Inefficiencies
Even brief production halts can be financially devastating. Common causes include equipment malfunctions, inefficient workflows, and material shortages.
- High repair and maintenance costs from unexpected failures
- Increased waste and scrap rates occur due to defective production
- Order delays impacting revenue and customer satisfaction
Optimization Strategy: IoT-enabled predictive maintenance detects early signs of equipment wear and tear, reducing downtime. ERP-driven real-time monitoring enhances workflow efficiency, ensuring seamless operations with minimal waste.
4. Regulatory Compliance and Legal Costs
Stricter global regulations on semiconductor manufacturing—from environmental sustainability to export restrictions—impose significant financial burdens. Non-compliance can result in hefty fines, legal disputes, and reputational damage.
Optimization Strategy: Automated compliance management tools within ERP systems streamline reporting, reduce administrative workloads, and ensure adherence to industry regulations. AI-driven risk assessment proactively addresses compliance challenges.
5. Labor Shortages and Workforce Training
The semiconductor industry faces a persistent talent gap, leading to higher recruitment and training costs. With advanced AI-driven manufacturing on the rise, the demand for specialized skills continues to grow.
Optimization Strategy: AI-driven automation reduces reliance on manual labor, while investing in upskilling programs significantly enhances workforce efficiency. Furthermore, smart manufacturing technologies streamline production, minimizing operational disruptions.
Future-Proofing Semiconductor Manufacturing for Cost Efficiency
To remain competitive, semiconductor manufacturers must adopt future-ready strategies:
1. Integrate AI and Automation
- Leverage AI-driven process optimization to enhance production scheduling and resource utilization.
- Reduce material waste and improve overall efficiency through automated quality control.
2. Leverage ERP for Data-Driven Decision-Making
- Utilize real-time analytics for cost monitoring, inventory control, and performance tracking.
- Enhance visibility into supply chain operations with integrated ERP solutions.
3. Strengthen Supply Chain Resilience
- Diversify supplier networks to mitigate risks from geopolitical and logistical disruptions.
- Invest in regional manufacturing hubs to ensure stable production and reduce lead times.
4. Enhance Sustainability Practices
- Transition to energy-efficient manufacturing and explore renewable energy sources.
- Implement waste reduction programs to optimize material usage and lower operational costs.
5. Adopt Predictive Maintenance
- Use IoT-powered sensors to monitor equipment health and prevent unexpected downtime.
- Implement AI-driven maintenance scheduling to optimize production efficiency.
Optimize Your Semiconductor Operations with Phitomas
Navigating the hidden costs of semiconductor manufacturing requires a strategic, technology-driven approach. At Phitomas, we specialize in AI-powered ERP solutions, predictive analytics, and smart automation to help semiconductor manufacturers reduce costs, enhance operational efficiency, and build resilient supply chains.
Let us help you optimize costs without compromising quality. Contact us today to learn how our intelligent manufacturing solutions can future-proof your semiconductor business.