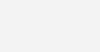
Nov 09 2023
/
Embracing Industry 4.0: Overcoming Challenges in Metal Fabrication
In the world of manufacturing, the metal fabrication industry stands as an enduring pillar, shaping everything from the vehicles we drive to the structures we inhabit. However, as the digital age unfolds, the metal fabrication sector is not exempt from the transformative winds of Industry 4.0. This article delves deep into the evolution of metal fabrication in the context of Industry 4.0, explores the challenges that arise in this transformation, and provides insights into overcoming these obstacles.
The Dawn of Industry 4.0 in Metal Fabrication
Before we dive into the challenges, let’s first understand what Industry 4.0 signifies for metal fabrication. Industry 4.0, often referred to as the Fourth Industrial Revolution, represents a confluence of technologies that is reshaping manufacturing at its core. It includes automation, the Internet of Things (IoT), artificial intelligence (AI), data analytics, and more.
Challenges of Embracing Industry 4.0
Embracing Industry 4.0 technologies in metal fabrication presents both opportunities and formidable challenges. Manufacturers are keen to reap the benefits of automation, real-time data analytics, and interconnected devices, but these come with their own set of hurdles.
1. Adaptation to Automation
One of the primary challenges is adapting to automation. While automated processes can significantly increase efficiency and reduce errors, the implementation of robotics and automated systems often requires significant capital investments. Moreover, it necessitates a change in workforce skills, as employees must be trained to work alongside machines effectively.
2. Data Overload and Analytics
The proliferation of sensors and IoT devices generates vast amounts of data. While this data can be a goldmine for optimizing processes and making informed decisions, it also poses a challenge in terms of data management, storage, and analysis. Manufacturers need robust data analytics capabilities to derive actionable insights from this deluge of information.
3. Cybersecurity Concerns
With the interconnection of devices and systems through the IoT, cybersecurity becomes a paramount concern. The more connected a system is, the more vulnerable it becomes to cyberattacks. Manufacturers must invest in robust cybersecurity measures and employee training to safeguard against potential breaches that could disrupt operations and compromise sensitive data.
4. Ensuring Quality Amidst Automation
While automation can enhance efficiency, ensuring consistent quality can be challenging. Machines can operate at high speeds, but maintaining product quality standards is crucial. Manufacturers need to implement quality control measures that align with automated processes to prevent defects and product recalls.
5. Workforce Transformation
The introduction of Industry 4.0 technologies demands a workforce transformation. Employees need to acquire new skills to operate and manage automated systems, interpret data, and address cybersecurity threats. Providing adequate training and fostering a culture of continuous learning is essential to overcome this challenge.
6. Scalability and Flexibility
Scalability is another challenge, especially for small and medium-sized enterprises (SMEs). Adapting and scaling up Industry 4.0 technologies can be resource-intensive. Manufacturers must plan for scalability from the outset and consider how these technologies can flexibly adapt to changing market demands.
Overcoming the Challenges
While these challenges are formidable, they are not insurmountable. The metal fabrication industry can overcome them through strategic approaches and investments. Here are some strategies to navigate these challenges effectively:
1. Investment in Workforce Development
Empowering the workforce with the necessary skills and knowledge is paramount. This includes training programs in automation, data analytics, and cybersecurity. Companies can collaborate with educational institutions to ensure a pipeline of skilled talent.
2. Integration of Data Analytics
To manage the data deluge effectively, manufacturers can invest in robust data analytics platforms. These tools can not only sift through vast datasets but also provide actionable insights to improve processes, quality, and decision-making..
3. Comprehensive Cybersecurity Measures
Robust cybersecurity measures, including firewalls, intrusion detection systems, and employee training, are essential. Regular security audits and updates should be conducted to stay ahead of evolving threats.
4. Quality Control Integration
To ensure product quality remains high in automated environments, quality control processes should be integrated with automation. Automated inspection systems can identify defects and deviations from quality standards in real-time.
5. Agile Implementation
Manufacturers should adopt an agile approach to implementing Industry 4.0 technologies. This involves starting with pilot projects, learning from them, and gradually scaling up as the organization becomes more comfortable with the technology.
6. Collaboration and Knowledge Sharing
Collaboration within the industry is vital. Manufacturers can benefit from sharing best practices, insights, and solutions to common challenges. Industry associations and forums can facilitate such collaboration.
7. Continuous Innovation
Finally, embracing Industry 4.0 is not a one-time effort but an ongoing journey. Manufacturers should continuously seek ways to innovate and optimize their processes, leveraging emerging technologies to stay competitive.
Conclusion
The journey to embrace Industry 4.0 in metal fabrication is marked by challenges, but it is also laden with opportunities for growth, efficiency, and innovation. Manufacturers that strategically invest in workforce development, data analytics, cybersecurity, quality control, and scalability will not only overcome these challenges but also position themselves as leaders in the evolving landscape of metal fabrication. The digital age has dawned upon this traditional industry, and those who adapt wisely will thrive in the era of Industry 4.0.