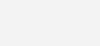
Jul 04 2025
/
Discrete Manufacturing ERP in Action: Transforming Production Efficiency and Visibility
Discrete manufacturing is complex. It involves building products made up of individual parts. Think about cars, smartphones, or airplanes. Each one needs thousands of components assembled just right. Managing all this can get messy fast. That’s where ERP systems come in.
ERP solutions are becoming more important too. They help cut costs, improve planning, and boost flexibility. Those benefits aren’t just ideas—they’re real. Companies already using ERP see faster delivery, fewer mistakes, and happier customers.
This article explores how ERP transforms discrete manufacturing. You’ll see stories from real factories. Discover how these tools make operations smoother and more efficient. Let’s dive into how ERP drives excellence in manufacturing today.
Understanding Discrete Manufacturing ERP Systems
What is Discrete Manufacturing ERP?
An ERP (Enterprise Resource Planning) system for discrete manufacturing is software that manages every step of making products. It tracks raw materials, schedules work orders, and controls quality. It pulls all data into one system, so everyone stays on the same page.
Unlike process manufacturing ERP, which handles items like chemicals or food that blend together, discrete ERP focuses on individual parts. Each item is unique, assembled in steps, and needs precise tracking.
Key Features of Discrete Manufacturing ERP
- Bill of Materials (BOM) Management: Keeps track of parts needed for each product. It helps avoid shortages or excess stock.
- Work Order and Routing Management: Plans the sequence of jobs. Ensures machines and workers are scheduled efficiently.
- Inventory and Supply Chain Integration: Monitors stock levels in real time. Connects suppliers, so parts arrive just when needed.
Benefits of Implementing ERP in Discrete Manufacturing
Companies see several key improvements after adopting ERP:
- Better production planning helps meet demand without overproducing.
- Traceability becomes easier, improving product quality.
- Efficiency increases, saving money and time.
Today’s manufacturers need these advantages to stay competitive in a fast-changing market.
Real-World Applications of Discrete Manufacturing ERP
Case Study: Automotive Industry
Car makers use ERP to manage complex assembly lines. They coordinate thousands of parts — from engines to seats. ERP helps achieve just-in-time inventory. This lowers storage costs and reduces delays. When a part arrives at the right moment, production flows smoothly. As a result, downtime drops and output rises.
Case Study: Electronics and Technology
Fast product cycles challenge electronics firms. They rely on ERP for rapid parts tracking and assembly. With real-time data, they spot issues early. Components are monitored at every stage, from supplier to final product. Quick response means getting new gadgets on shelves faster.
Case Study: Aerospace and Defence
Airplane manufacturers face strict rules. ERP helps ensure compliance through detailed documentation. They also streamline procurement and engineering change processes. When changes happen, ERP makes sure everyone follows new standards. This reduces errors and guarantees safety.
Core ERP Modules Powering Discrete Manufacturing
Production Planning and Scheduling
Using dynamic tools, manufacturers can adapt schedules to meet demand shifts. They can run different scenarios and plan for unexpected delays. This keeps production running smoothly, even when surprises happen.
Inventory and Supply Chain Management
Real-time stock updates let companies keep minimal inventory. Automated orders fill gaps without overstocking. Supplier portals enable better collaboration, making procurement faster and more reliable.
Quality Management and Compliance
Quality modules include inspection checklists and testing records. They help catch defects early. Plus, ERP helps prepare compliance reports and audit documents. This keeps certified standards met with less stress.
Maintenance and Asset Management
Preventive maintenance schedules avoid machine breakdowns. Predictive tools can even warn when a part is likely to fail. Tracking machine performance extends equipment lifespan and cuts repair costs.
Implementing ERP in Discrete Manufacturing: Best Practices
Planning and Needs Assessment
Start by analysing gaps in current processes. Define what needs improving. Get input from suppliers, managers, and operators. Clear goals guide a successful ERP rollout.
Selecting the Right ERP Solution
Choose software that can grow with your company. Look for specific features suited to your industry. Check how well it will integrate with your existing systems. A good fit ensures smooth adoption.
Change Management and User Adoption
Training is critical. Offer hands-on support to help staff learn new workflows. Address resistance early by showing how ERP makes everyone’s work easier. Stakeholder support accelerates the process.
Continuous Improvement and Optimization
ERP isn’t a one-time project. Regularly review performance. Update systems and add new features. Use data insights to improve processes steadily.
Future Trends in Discrete Manufacturing ERP
Integration with IoT and Industry 4.0
Connected sensors and devices make operations smarter. Real-time data from machines helps identify issues fast. This leads to more automation and fewer errors.
AI and Machine Learning Enhancements
AI predicts when machines need maintenance. It helps improve quality by identifying patterns. Automating repetitive tasks frees workers for more strategic roles.
Cloud-based ERP Solutions
Cloud options offer scalability and remote access. Teams can collaborate from anywhere. There are security challenges, but with good practices, cloud systems keep data safe and accessible.
Conclusion
ERP systems are changing how companies run discrete manufacturing. They improve planning, boost quality, and lower costs. Success depends on choosing the right system and managing change well.
Now’s the time to evaluate your current processes. Find areas where ERP can make an immediate difference. Staying competitive means embracing these tools. With a strategic approach, your manufacturing operation can become more agile, transparent, and ready for future growth.