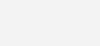
Mar 07 2025
/
Semiconductor Supply Chain Challenges? Strategies for Resilience and Growth
Semiconductor Supply Chain Struggles? Here’s What You Need to Know!
The semiconductor industry powers everything from smartphones to automobiles, but recent supply chain disruptions have sent shockwaves across global markets. Manufacturers are grappling with unprecedented production delays, skyrocketing costs, and uncertain lead times, making it crucial for businesses to rethink their supply chain strategies.
If you’re in the semiconductor industry—whether as a manufacturer, distributor, or stakeholder—understanding these challenges and adopting proactive, technology-driven solutions is key to maintaining competitiveness. In this article, we break down the biggest roadblocks in semiconductor supply chains and explore practical strategies to build resilience and ensure uninterrupted operations.
The Biggest Challenges in the Semiconductor Supply Chain
1. Global Semiconductor Shortage
The demand for semiconductors has surged due to advancements in AI, IoT, and 5G technology. However, supply chains have struggled to keep up due to:
- Limited production capacity at foundries – Major foundries like TSMC and Samsung operate at maximum capacity, making it difficult to meet global demand.
- Increased demand from multiple industries – Automakers, consumer electronics, and cloud computing sectors all compete for the same limited semiconductor resources.
- Geopolitical trade restrictions impacting supply – Export bans and trade wars between countries have created bottlenecks in semiconductor shipments, affecting global supply chains.
2. Raw Material Constraints
Semiconductor manufacturing relies on rare materials like silicon, gallium, and neon gas. Disruptions in their supply can lead to:
- Increased production costs – Limited availability of key raw materials drives up prices, increasing manufacturing expenses.
- Production slowdowns – Shortages of critical components can cause unexpected downtime, affecting output and delivery timelines.
- Environmental regulations – Stricter policies on mining and resource extraction further constrain access to essential raw materials.
3. Logistics Bottlenecks
Transportation delays and labor shortages in key global trade hubs have impacted the timely delivery of semiconductor components, leading to:
- Extended lead times – The time required to move components from suppliers to manufacturers has increased significantly, delaying product launches.
- Increased shipping costs – The rise in demand for freight services has caused shipping fees to skyrocket, impacting overall production budgets.
- Risk of production shutdowns – Late deliveries of critical components can force factories to halt operations, leading to revenue losses and backlogs.
4. Geopolitical & Regulatory Challenges
Trade tensions and government-imposed restrictions have forced manufacturers to reassess their supply chain strategies. Challenges include:
- Export controls and tariffs – Restrictions on technology exports and high tariffs on semiconductor components have disrupted global trade.
- Regional manufacturing policies – Countries are investing in local semiconductor production, shifting global supply chain dynamics.
- Intellectual property (IP) protection – Stricter regulations on semiconductor technology transfer affect partnerships and innovation.
5. Limited Manufacturing Capacity & Foundry Dependence
Many semiconductor companies rely on a handful of foundries, such as TSMC and Samsung. Any disruption in these facilities can lead to:
- Global supply shortages – A single event, such as a natural disaster or factory shutdown, can cripple semiconductor availability worldwide.
- Price volatility – Limited production capacity can drive up chip prices, affecting manufacturers and end-users.
- R&D investment gaps – Dependence on external foundries limits in-house innovation, making companies reliant on third-party advancements.
Strategies to Overcome Semiconductor Supply Chain Disruptions
1. Diversifying Supplier Networks
Relying on a single supplier or geographic region increases risk. Manufacturers should consider:
- Multi-sourcing strategies for key components – Engaging with multiple vendors to avoid dependency on a single supplier.
- Partnering with regional suppliers – Working with local manufacturers to ensure continuous supply.
- Investing in local semiconductor production facilities – Building or partnering with fabs in different regions to reduce supply disruptions.
2. Leveraging Predictive Analytics & AI
AI-driven supply chain analytics can help predict demand fluctuations and optimize inventory management. Benefits include:
- Identifying potential bottlenecks before they occur – AI can analyze historical data to foresee supply chain disruptions.
- Optimizing procurement schedules – Automated systems ensure timely ordering and replenishment of materials.
- Reducing waste and excess inventory costs – AI helps companies maintain lean inventory levels without overstocking or understocking.
3. Strengthening Supply Chain Resilience with Digital Solutions
Smart ERP and supply chain management (SCM) software, such as Infor CloudSuite Industrial, can help semiconductor manufacturers:
- Gain end-to-end visibility of their supply chain – Real-time tracking of inventory, shipments, and production progress.
- Automate procurement and inventory tracking – Reducing manual errors and improving efficiency.
- Improve supplier collaboration and risk mitigation – Streamlining communication and ensuring supply continuity.
4. Investing in Onshore & Nearshore Manufacturing
Companies are increasingly adopting a regionalization approach by bringing production closer to key markets. Advantages include:
- Reduced reliance on offshore facilities – Mitigating risks associated with international supply chain disruptions.
- Lower transportation costs – Shorter shipping distances mean lower expenses and faster deliveries.
- Increased control over production quality – Closer proximity allows for better oversight of manufacturing processes.
5. Enhancing Risk Management Strategies
To mitigate disruptions, businesses should:
- Develop contingency plans for critical components – Ensuring alternative sourcing options are available.
- Maintain buffer stock for high-risk materials – Keeping reserve inventory to counteract supply shocks.
- Implement dynamic supplier qualification processes – Regularly assessing supplier reliability and diversifying sourcing options.
The Future of Semiconductor Supply Chains
Looking ahead, the semiconductor industry must adopt smarter, more agile supply chain models to navigate uncertainty. Companies that embrace AI-driven analytics, ERP solutions, and supplier diversification will be better positioned to handle future disruptions.
How Phitomas Can Help
At Phitomas, we specialize in intelligent manufacturing solutions that empower semiconductor companies to:
- Optimize supply chain management with AI-powered ERP systems
- Improve production efficiency through automation and smart analytics
- Enhance risk mitigation with advanced forecasting tools
To learn more about how Phitomas can transform your semiconductor operations, contact us today!
Stay Ahead of the Curve
The semiconductor industry’s supply chain challenges are complex but manageable with the right strategies. By diversifying suppliers, leveraging AI-driven insights, and strengthening digital infrastructure, companies can overcome disruptions and secure long-term growth.
Future-proof your semiconductor supply chain today!