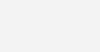
Oct 02 2023
/
The Role of IIoT in Modern Industrial Equipment Manufacturing
In today’s rapidly evolving industrial landscape, the relentless pursuit of cutting-edge technology has sparked a profound revolution in the design, construction, and operation of industrial equipment. One technology at the forefront of this transformation is the Industrial Internet of Things (IIoT). Over just a few years, IIoT has risen from relative obscurity to take center stage, significantly impacting how industrial equipment is conceived, manufactured, and managed. This article is dedicated to exploring the multifaceted world of IIoT, delving into its critical significance in manufacturing, its diverse array of benefits for industrial processes, and a compelling range of real-world examples that highlight its seamless integration and resounding success.
Introduction to IIoT and its Significance in Manufacturing
The Industrial Internet of Things, abbreviated as IIoT, is a pioneering force that has brought together industrial machinery and devices with the vast potential of the internet. At its core, IIoT represents an intricate web of interconnected equipment, sensors, and sophisticated software solutions. These components are meticulously engineered to facilitate real-time data exchange, remote monitoring capabilities, and the application of data-driven, intelligent decision-making within the expansive realm of manufacturing.
IIoT empowers machinery, factories, and entire industrial ecosystems with the ability to communicate, analyze, and adapt in a digital language. It transforms ordinary industrial equipment into smart, interconnected entities capable of conveying their status, performance, and requirements to human operators and even to other machines. The significance of this monumental shift cannot be overstated. It has ushered in an era where every facet of industrial equipment manufacturing is marked by enhanced efficiency, optimized operations, and data-informed decision-making.
Significance of IIoT in Manufacturing: A Paradigm Shift
The emergence of the Industrial Internet of Things (IIoT) has triggered a profound transformation in modern industrial equipment manufacturing. This heralds a new era where traditional machinery has evolved into intelligent, interconnected systems. The significance of IIoT in this realm is nothing short of revolutionary, and it owes its transformative power to a constellation of compelling reasons.
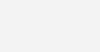
1. Enhanced Connectivity: Breathing Life into Machines
At the heart of IIoT lies its remarkable capacity to foster enhanced connectivity. This goes beyond mere data transmission; it represents the weaving together of industrial machinery, sensors, and software into a collaborative, interconnected ecosystem. This dynamic web of interconnected components enables manufacturers to seamlessly monitor and control equipment, regardless of geographic boundaries. IIoT empowers machinery to ‘speak’ and collaborate with each other and their human overseers. This unprecedented connectivity enhances productivity, enables remote management, and facilitates agile responses to unforeseen challenges.
For instance, imagine a vast steel manufacturing plant using IIoT to monitor its massive blast furnace. Sensors continually provide data on temperature and pressure to a central control system. If the system detects even a subtle deviation from optimal conditions, it can instantly and autonomously trigger corrective actions, such as adjusting temperature controls or altering the mixture of raw materials. The result? Precision that ensures consistent product quality and minimizes energy waste.
2. Benefits of IIoT in Enhancing Production Efficiency
IIoT serves as an incessant source of data from machinery and production processes. If harnessed effectively, this data deluge can revolutionize decision-making within manufacturing operations. Real-time insights into machine performance, production efficiency, and product quality become readily available, empowering manufacturers to make informed decisions and optimizations.
Consider an automotive assembly line where IIoT sensors monitor every aspect of the production process. Data on cycle times, error rates, and energy consumption is continuously gathered and analyzed. With this information, manufacturers can identify bottlenecks in real-time, adjust production pace, or reconfigure the assembly line layout for maximum efficiency. Data-driven decision making ensures resource optimization, minimizes operational costs, and maintains consistent product quality.
3. Benefits of IIoT in Reducing Downtime
One standout advantage of IIoT is its capacity for predictive maintenance. By constantly monitoring equipment health, IIoT systems can predict when a machine is likely to fail. This proactive approach enables manufacturers to schedule maintenance well in advance of a potential breakdown, minimizing downtime and significantly reducing maintenance costs.
Imagine a factory producing heavy machinery. IIoT sensors meticulously track critical components, monitoring factors such as temperature, vibration, and lubrication status. When the system detects anomalies suggesting impending issues, it promptly triggers alerts. Maintenance teams can then take action, addressing the problem before it escalates into a costly and disruptive breakdown. The result is a remarkable reduction in unplanned downtime, ensuring that production lines operate with efficiency.
4. Benefits of IIoT in Optimizing Operations
IIoT’s automation capabilities extend beyond data gathering; they encompass routine task execution. This reduces the need for manual intervention, enhancing operational efficiency and reducing the risk of human error. The result is a smoother, more efficient production process that consistently delivers high product quality.
For instance, in a food processing plant, IIoT can oversee temperature and humidity control in storage facilities. When sensors detect fluctuations outside the optimal range, the IIoT system can autonomously adjust conditions to prevent spoilage, preserving product quality and reducing waste.
These four pillars of IIoT’s significance in manufacturing, namely enhanced connectivity, data-driven decision making, predictive maintenance, and improved efficiency, have set the stage for a manufacturing renaissance. Yet, this is just the beginning. As we continue our exploration, we will dive deeper into the specific benefits that IIoT brings to the realm of industrial equipment manufacturing. We will explore how IIoT enhances production efficiency, minimizes downtime, and optimizes operations. We will also journey through real-world exemplars, where companies like Caterpillar Inc., General Electric, and Siemens AG have harnessed the transformative power of IIoT to reshape the landscape of industrial equipment manufacturing. These examples will serve as vivid testaments to IIoT’s potential as a catalyst for progress and innovation in this ever-evolving arena.
Benefits of IIoT in Real-world Industrial Equipment Manufacturing
To fully appreciate the impact of IIoT in the manufacturing of industrial equipment, it’s crucial to examine real-world examples of its successful implementation. Let’s delve into the stories of companies that have harnessed the power of IIoT to revolutionize their manufacturing processes and achieve remarkable results.
1. Caterpillar Inc.: Pioneering Remote Equipment Monitoring
Caterpillar, a renowned manufacturer of construction and mining equipment, has embraced IIoT to optimize its machinery. They use remote monitoring through IIoT sensors to keep tabs on the health of their equipment, including engines and hydraulic systems.
When a piece of machinery sends an alert indicating a potential issue, Caterpillar’s service technicians can remotely diagnose the problem and, in many cases, resolve it before it causes downtime. This not only minimizes equipment downtime but also enhances customer satisfaction by ensuring that Caterpillar’s equipment operates reliably.
2. General Electric (GE): Powering Up Wind Turbines with IIoT
GE is a prime example of a company leveraging IIoT in the manufacturing of industrial equipment. They’ve developed a platform called “Predix” that combines sensors, data analytics, and machine learning to optimize industrial processes.
For instance, GE’s Predix platform is used in wind turbines. Sensors installed in the turbines collect data on factors like wind speed, temperature, and vibration. This data is then analyzed in real-time to make adjustments that optimize power generation and reduce maintenance costs. As a result, wind farm operators can increase energy output while decreasing operational expenses.
3. Siemens AG: The Innovation of Digital Twins
Siemens, a multinational conglomerate, employs IIoT in various aspects of its manufacturing processes. They have introduced a concept called “Digital Twins,” where virtual replicas of physical machines are created and continuously updated with real-time data from sensors.
This approach allows Siemens to monitor the performance and health of their industrial equipment in real-time. By simulating different operating conditions and scenarios, they can optimize machine performance and predict maintenance needs accurately. This ensures that their equipment operates efficiently, and customers experience minimal downtime.
Conclusion: IIoT’s Transformative Power in Industrial Equipment Manufacturing
The Industrial Internet of Things (IIoT) has transcended its status as a mere technological trend to become a driving force behind a manufacturing revolution. Its ability to enhance connectivity, enable data-driven decision making, predict maintenance needs, and improve operational efficiency has positioned it as a game-changer in industrial equipment manufacturing.
As we’ve seen through real-world examples, IIoT isn’t just a concept; it’s a practical solution that delivers tangible results. Companies like Caterpillar Inc., General Electric, and Siemens AG have harnessed IIoT to reduce downtime, enhance product quality, and optimize operations. These successes underscore the immense potential of IIoT to reshape the landscape of industrial equipment manufacturing and drive progress and innovation in this ever-evolving industry.
In conclusion, IIoT isn’t merely a technological tool; it’s a transformative paradigm that has already left an indelible mark on modern manufacturing. As technology continues to evolve, it’s certain that IIoT will play an even more pivotal role in shaping the future of industrial equipment manufacturing, driving efficiency, and innovation to new heights.